Supplier Collaboration ... understanding Total Cost Of Procurement (TCOP)
- Richard Kunst
- Apr 18, 2021
- 5 min read
When sourcing and developing long-term supplier relationships on MRO* or production items, the Total Cost Of Procurement (TCOP) checklist below can help to:
Identify which customized services and guarantees to request in exchange for long-term commitments;
Guide an inter-departmental, materials-management task team in re-thinking and re-structuring the flow of materials, paper and information to achieve three levels of productivity-efficiency, effectiveness, and structural or transformational.
WHAT IS TCOP?
When a firm buys items that are not instantly consumed there are two main categories of procurement costs - buying and holding; they, in turn, can be subdivided into the following checklist:
BUYING COSTS HOLDING COSTS
1. Price 7. Storage space cost
2. Shopping time 8. Financing of inventory
3. Paperwork 9. Control
4. Expediting 10. Shrinkage
5. Mistakes 11. Taxes, Insurance (Misc.)
6. Internal Handling to final consumption point
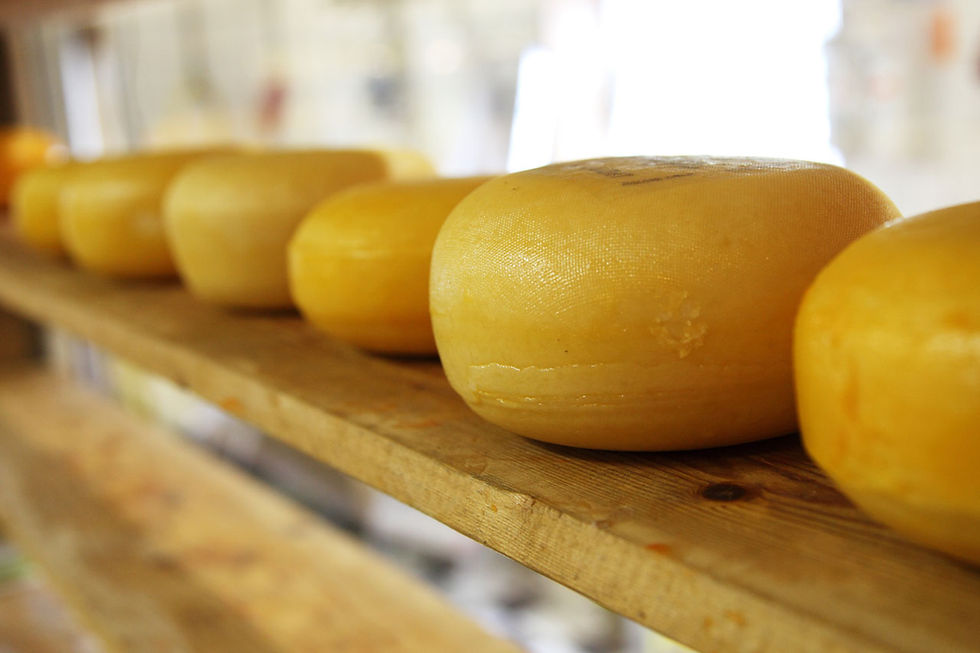
This checklist suggests that when buying something there are six separate costs that may be incurred to get physical goods to their final storage-usage point. Price (#1) is the only instantly measurable element of the 11. To get a good price requires comparative shopping and negotiating time (#2) which is expensive if purchasing department overhead is included in the hourly rate of its personnel. For every purchase, paperwork (3#) is generated. If the goods arrive at the wrong time, place or specs, then the costs of expediting and mistake-curing (#4,5) are incurred; "mistakes" should also include the downtime costs of other deprived departments. Goods are often delivered to a general receiving area instead of the final consumption-storage point; this requires internal handling and paperwork costs (#6).
Once goods get to their final storage point, buying costs stop and holding costs start. Inventory ties up space and capital (#7,8). Then it must be watched, counted, moved, etc.-housekeeping, control costs (#9). If while waiting to be used, it is damaged, permanently borrowed, or becomes obsolete, the investment must be written off "shrinkage" (#10). And finally, the overall, average investment in inventory must be insured and taxed (#11).
Using the checklist, all of the TCOP elements can be lowered if not eliminated - here is how:
Start with #1; want the best price? Offer all of your volume on a class of goods to one supplier, and ask for prices for differing lengths of commitment. If a supplier can count on predictable volume, then they can plan their business more efficiently to give you not only a volume discount but a cooperative economics discount too. If you get married to one type of supplier, then the shopping time (#2) could drop nearly to zero. Wal-Mart has, for the past few years, been requesting that suppliers eliminate outside salespeople and pass the commission on at a lower price. Presumably, they would be willing to pay for the cost of a sales representative on an as-needed-to-see basis.
Paperwork (#3) would naturally consolidate with the elimination of duplicate suppliers, but the ultimate step would be to request sole suppliers to accept orders through EDI* and to bill back the same way. Paperless, electronic ordering and billing are becoming a standard customized service request at places like GM in order to minimize these costs.
Expediting(#4) and Mistakes(#5) should go to zero if you pick the best service-providing supplier and request perfect on-time and accurate shipments in exchange for the marriage commitment. If the supplier does occasionally slip, then agree on appropriate penalty fees which would offset the internal costs. Most suppliers boast about service, but by requesting unconditional service guarantees and setoff fees, only best-service suppliers remain.
Internal handling costs (#6) can be eliminated if both parties can change to have direct-to-the-consumption-point delivery. If this requires the supplier to make more and smaller deliveries, then their delivery costs will escalate and the price must be raised. Together find the optimal order size that lowers internal handling and all holding costs more than the price goes up due to the extra delivery costs.
All holding costs (7-11) approach zero if a supplier delivers goods just-in-time, and there are many documented cases for this with manufacturing components.
When applying the TCOP model, three common pitfalls are:
Looking at the short-term, fixed costs of storage space- "we own or lease the space to be freed, so we won't save there;" and the semi-fixed aspect of other costs. Remember, though, this type of purchasing is a long-term, re-structuring proposition; in the long-term all costs are variable.
If just-in-time works well for manufacturing components, then why not for MRO items. Because the dollar amounts and space requirements for MRO items are usually small, the holding costs are not that significant. What is more important are the buying costs and the supplier's transactional and delivery costs. If the relationship is to be a long-term, win-win deal, then the supplier's delivery costs must be covered which will offset the holding-cost savings. If MRO inventory is turning over 3 times per year, work with suppliers to get 12 turns, but don't expect to get magnitudes of 20 to 100 turns per year.
If a cost can't be seen or hasn't been measured, it is assumed to be negligible. Items 2-11 of the TCOP checklist are collectively referred to as "hidden costs;" out of sight is out of mind. Those who measure these costs fully and honestly for the first time are always unpleasantly surprised.

THREE LEVELS OF PRODUCTIVITY?
Look for three dimensions of productivity within any new purchasing relationship:
Efficiency- do the same activities with more automation and less waste;
Effectiveness-on top of efficiency, look for ways to add additional value. For example, computerized inventory control systems have made reordering more time-efficient, but also effective by lowering investment in inventory while boosting fill rates and allowing different departments and divisions to source needs already in-house instead of buying duplicate items.
Transformational or structural productivity- this occurs when the underlying systems that organize and coordinate people and materials are redesigned to yield higher orders of economics. An article in Business Week mentioned that one of the auto companies now issues checks for goods at the receiving dock which allowed many people in payables to be redeployed as well as an additional fast-pay discount from the suppliers. This firm has added the payables step onto the end of the buying cost list in the TCOP model.
Total Cost Of Procurement (TCOP) – Report Card and Improvement Agenda
Typically a particular supplier will get tagged as being a horrible supplier to deal with, quality and delivery issues. Often the supplier is unfairly judged, typically as a result of the volume of product they supply. Here is where TCOP is a great tool. It contains both a subjective and quantitative evaluation of your supplier. The TCOP Report captures subjective results related to Quality, Delivery, Service and Cost and then quantifies them for every $1,000 of annual spend conducted with that supplier. The TCOP report also works as an excellent working agenda with your suppliers on the path of improvement. I recall using the report to eliminate the confusion of on-time delivery … supplier thought our request date meant their ship date when it was our required dock date … the result was an overall 3-day reduction of our on-hand inventory.
Doing the inverse of TCOP to measure your relationship with your customer works equally as well to reduce disturbances to flow and a cooperative attitude to reducing relationship overhead costs providing for a more competitive strategy.
CONCLUSION
If a firm were to use the TCOP model to lower price and zero out most of the other costs, a structural transformation would occur. All of the activity areas touched would be downsized freeing up people's time to pursue higher-level skills and responsibilities. Such a program would require conscious strategic and total material management process decisions. No one area can make these decisions or make a total program work; such a program would require an inter-departmental task team with top management's blessing.
Many progressive firms today are looking for bottom-up ideas and initiatives to achieve new magnitudes of productivity which by definition liquidate old job activities and create new ones. The TCOP model can be a guide for re-thinking supplier agreements and for re-thinking the entire material management process.
Comments